In two labs of the Titu Technical Center, located 45 minutes northeast of Bucharest (Romania), the brand’s engineers rigorously test the quality and resistance of the interior and exterior materials of all models.
Famous for their accessibility, Dacia vehicles are also known for the robustness of their elements. It is not uncommon to see Logan and Duster vehicles with thousands of miles on the odometer.
This fame is not the result of chance. The secrets of the Dacia’s longevity are kept in two labs at the Titu Technical Center, 45 minutes northeast of Bucharest, Romania. There, the brand’s engineers test the quality and resistance of the interior and exterior materials of all models.
The Titu Technical Center is located near Bucharest. Opened in 2010, this ultra-modern complex is located in the heart of the Romanian countryside. With 600 people, 300 hectares and a network of outdoor test tracks, it has everything it takes to guarantee the quality of the new vehicles developed by Dacia. The center houses two laboratories dedicated to the durability of materials, where they are subjected to accelerated aging tests. In just a few weeks, life years under different climatic conditions are simulated, the result of which in each sample of each material will be analyzed in detail by passionate experts. Welcome!
We start the visit in the center of sustainability of polymers and liquids. Among the tested parts are, of course, those made of plastic. Manufactured and molded in many different ways, this material is an important part of the vehicle interior. From the dashboard to the gearbox to the doors, it’s everywhere! And of course, if it’s not of good quality, much of the vehicle can deteriorate over time.
“But it’s not just the passage of time that can affect the durability of materials. Exposure to extreme temperatures is a key factor that is especially important in Spain. We have to guarantee that our plastics can withstand many hours under the Cadiz sun or thermal jumps of more than 20 degrees at certain times of the year,” says Fernando Vara, after-sales and quality director at Dacia Iberia.
In this laboratory, opened in 2017, Nicoleta analyzes the impact that atmospheric conditions and the different applications can have on the appearance and quality of the pieces. For example, UV rays, heat and bad weather can turn white, cause color loss or change the clarity of the plastic.
Every day, dozens of samples are placed in the laboratory tanks under UV for up to 3,000 hours. Thus, the pieces absorb radiation equivalent to several years of sun exposure. In addition, they spend several weeks in huts where they are exposed to extreme temperatures and humidity ranging from -40° to +100°. The goal is to check resistance in all environments. At the end of these shock treatments, the pieces are analyzed and compared with a control sample without aging.
The appearance of the plastic is also threatened by the simple handling of the vehicle. For example, a bicycle, keys or a ring can also cause damage and leave permanent marks on the bodywork or on part of the passenger compartment. To prevent this, all plastics undergo the attack of a “torture” instrument designed to simulate scratching. Specifically, it is a metal screw that is cruel to the monster and moves back and forth in length and width. Scratches, which are unavoidable, should remain superficial and should not alter the properties of the plastic.
Over time, the pieces can also warp, wrinkle and even break. So in the lab of durability of polymers and fluids, a traction machine’s mission is to stretch the plastic to test its resistance to breakage. Only materials that pass all tests are selected.
Titu houses another laboratory: the corrosion center, opened in 2015. There, all metal parts are carefully examined thanks to an accelerated corrosion chamber. On a new vehicle, the paint protects the metal. But due to an accident or a scratch that damages the paint to the metal, it is exposed to corrosion.
In addition to small samples, complete parts such as the hood, tailgate, doors and dolly are also subjected to this test. Chrome and galvanized parts such as drums, brake discs, bolts and emblems are also checked. They are immersed in the corrosion chamber in extreme climatic conditions where the temperature, humidity and even the composition of the air vary. When leaving this chamber, the corrosion around the scratches is analyzed thanks to a very precise measuring instrument.
«This way we can guarantee the durability of our metal parts in the most aggressive environments. An essential factor in a country with thousands of kilometers of coastline, which is also home to some of the cities with the largest fleet of vehicles,” added Fernando Vara, After Sales and Quality Director of Dacia Iberia.
In addition to simulating natural conditions, chemical products are used to reproduce the aggressions in the car body. Using another special tool next to the corrosion chamber, the metal elements are brought into contact with, for example, windshield washer fluid or a de-icing salt solution.
To see the rest of the evidence, you have to cross a hallway that leads to another room where gravel is being removed, a procedure the name of which leaves little room for confusion. This method consists of projecting gravel onto a piece of metal under high pressure to assess the damage to the bodywork. Painting, chrome plating, galvanizing, etc., all protective layers are evaluated to ensure the best quality for vehicles.
“After successfully passing this series of tests, the parts and materials will be validated and can then be integrated into the new Dacia vehicles. At Dacia, we think about the longevity of our vehicles and reinforce them with a maintenance and verification program of checkpoints with a single goal: to enable every owner, why not, reach the million kilometers with their heads held high,” emphasizes the After Sales and quality director of Dacia Iberia, Fernando Vara.
Source: La Verdad
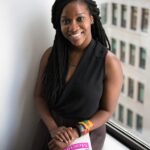
I am Ida Scott, a journalist and content author with a passion for uncovering the truth. I have been writing professionally for Today Times Live since 2020 and specialize in political news. My career began when I was just 17; I had already developed a knack for research and an eye for detail which made me stand out from my peers.