Rail is an environmentally friendly means of transport and ÖBB wants to invest around 28 billion euros in rail expansion by 2027. However, more train traffic also means more track construction and maintenance, which is not always environmentally friendly. According to a study by the Technical University of Graz, switching to alternative drive systems for the necessary machines can significantly reduce harmful emissions and contribute to achieving climate goals.
Whether grinding rails or renewing the track body: safe railway operation requires regular maintenance and renewal measures of the rail infrastructure. This requires huge special construction machines, most of which are powered by diesel engines. According to a broadcast from TU Graz, large groups of track construction machines, which can reach a length of several hundred meters, need up to 1000 liters of diesel per kilometer of track to be processed. According to the Institute of Railway Engineering and Transport Economics at the Graz University of Technology, 9,600 tonnes of CO2 equivalents are produced annually by ÖBB’s track maintenance operations.
Study proves: green track construction machines possible!
In a study, the Institute for Railway Engineering and Transport Economics of the Graz University of Technology, together with the manufacturer of railway construction machines Plasser & Theurer (Vienna/Linz), investigated the possibilities of reducing emissions and searching for suitable alternative drive technologies.
In addition, as part of a project with the German Center for Railway Research (DZSF), the institute analyzed the entire fleet of approximately 3,000 emergency vehicles in Germany in order to develop an optimal conversion scenario to alternatively powered machines. The research results confirm the applicability of alternative drive systems for track maintenance machines.
Based on a calculation program (CalCAS, Calculation of Comparison for Alternative Solutions) developed at the Technical University of Graz, several solutions were found: According to this, as many as 35 percent of the huge machines could cover their energy supply electrically – via the overhead wires. “In any case, the most energy-efficient solution,” says Matthias Landgraf from the Institute for Railway Engineering and Transport Economics at the Graz University of Technology.
Plasser & Theurer with the first hybrid track construction machines
For track construction machines with an energy requirement of up to 800 kilowatt hours (kWh), battery solutions already exist in the form of hybrids with overhead wires for charging. In 2015, Plasser & Theurer opened a new chapter in drive technology in railway construction: as the first manufacturer of railway construction machines, devices with hybrid drive technology were installed on rails.
For machines of more than 800 kWh, the experts consider a drive using hydrogen fuel cell technology to be optimal. Existing devices can temporarily use bio or synthetic fuels and in the medium term liquid hydrogen in combination with an internal combustion engine.
Railway companies are becoming increasingly aware of the need to prevent pollution. As Plasser & Theurer has already announced, ÖBB will be supplied with 56 low-emission, high-tech maintenance vehicles worth approximately EUR 250 million. The ÖBB wants to use it to modernize their fleet, which is about 30 years old.
Source: Krone
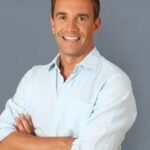
I’m Ben Stock, a journalist and author at Today Times Live. I specialize in economic news and have been working in the news industry for over five years. My experience spans from local journalism to international business reporting. In my career I’ve had the opportunity to interview some of the world’s leading economists and financial experts, giving me an insight into global trends that is unique among journalists.