“Modern factories are an industrial Tower of Babel”, this is how the tour of the Renault Refactory in Flins (France) began, a center where the manufacturer focuses on the circular economy of its own end-of-life vehicles. A similar project has started in Seville, with the aim of having it fully operational by 2024.
To try to discern the huge amount of data produced in the factories, Renault has made sure that all productive elements, from the machines to the operators, have a virtual identification in order to create a cybernetic environment in which it is more efficient to run processes design, debug and fix.
The diamond brand is equipping all its factories with a new global telecommunications network, so that the directors of the factories in France can see in real time what is happening in Palencia, for example.
This has led to the
“Manufacturing Control Tower”an element that coordinates the billions of data generated daily by its 10,000 energy sensors – which can see how much electricity each machine is receiving, optimal for pre-emptive fault finding – and the 7,000 hectares of Wi-Fi available in its factories.
This not only improves the operation of Renault’s international logistics chain, which uses the sensors present in the vehicles themselves – for example, it determines the optimal number of checks on the state of charge of a battery – but also, according to his estimates, generates savings between the 20% and 30% CO2 emissions.
In the words of the company itself, which has already implemented the transition of all its factories: “Valladolid and Palencia are at the forefront of digitalization throughout the Renault Group.”
Creating a virtual environment with identifiers for each productive element opens up the possibility of developing two essential elements for any chain: the formation and design of new elements from scratch.
At this last point, for example, theoretical material tests can be carried out before they are taken to the assembly line. With the help of these systems it was possible to optimize the paint systems and improve the properties of various elements, such as increasing the rigidity of the chassis and reducing the weight.
However, the real horizon in which manufacturers are trying to move forward is that of the chemical composition of batteries for electric cars. Last week, Bosch announced an agreement with IBM to use the latter’s quantum computers to achieve just that goal.
One of the most exciting departments at Renault is multijet fusion additive manufacturing, the most advanced form of 3D printing. This business area is responsible for designing complex structures to introduce them into the group’s models, although they can also use their foam as padding for seats.
In terms of training, working in digital environments through virtual reality, a saving on material for this purpose can be achieved, where it is most clearly visible in the painting departments.
Source: La Verdad
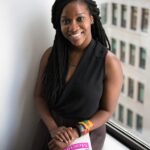
I am Ida Scott, a journalist and content author with a passion for uncovering the truth. I have been writing professionally for Today Times Live since 2020 and specialize in political news. My career began when I was just 17; I had already developed a knack for research and an eye for detail which made me stand out from my peers.